When you walk into a store and pick up a product, such as a new sweater, it’s easy to forget the journey it went through.
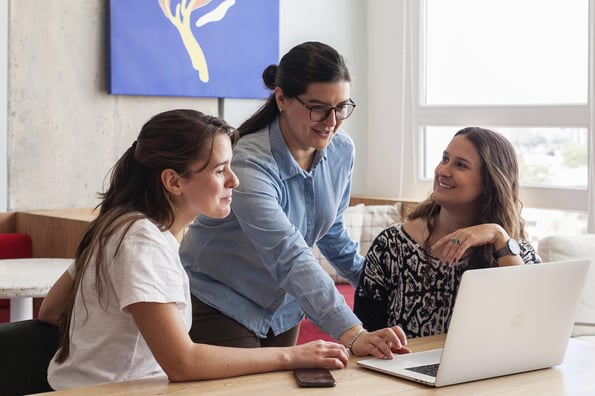
The sweater may have begun as a bundle of wool in New Zealand before being turned into fabric, sewn together, and shipped to the store.
For business owners, understanding the process of turning raw materials into finished products is essential.
The supply chain process has many moving parts that have to work together seamlessly to ensure customer satisfaction. As the backbone of any business, it needs to operate more like a well-oiled machine instead of a patchwork of steps.
What is a supply chain?
A supply chain is the entire network of people, resources, and organizations involved in turning raw materials into a finished product that goes to the customer.
What is the supply chain process?
The typical supply chain process includes the following links (or nodes): raw material supplier, manufacturer/processor, distributor, retailer, and customer.
This process moves in one direction (known as downstream). Raw materials flow through the supply chain and become a final product that the consumer purchases.
These links are connected by logistics that move materials and finished products from one node to the next.
Supply chain process example
Here’s an example of who plays the role of each link in the supply chain for a bag of coffee you purchase from the grocery store:
- Raw material suppliers: Farms where the coffee beans are grown and harvested.
- Processors: Processing plant where the excess pulp is removed from the beans.
- Distributor: Wholesale roasters that purchase green coffee beans, roast them, and package them in their branding.
- Retailer: The grocery store that purchases coffee from wholesale roasters to sell.
- Consumers: The end customers who purchase the bag of coffee at the grocery store.
Supply chain process management
Supply chain management (SCM) refers to the steps you take to manage the flow of goods and the processes that result in your final product.
Activities in supply chain management include:
- Keeping track of materials and goods in the supply chain.
- Collaborating with suppliers to optimize the flow of goods.
- Analyzing and optimizing sourcing processes.
- Monitoring supply chain performance.
- Tracking and maintaining inventory.
- Preventing disruptions.
The goals of supply chain management typically include avoiding product shortages and keeping costs down as items move from one node to the next.
Doing so helps you create a competitive advantage by delivering maximum value to your customers, ensuring product availability, and making speedy deliveries.
Many companies manage supply chain operations with enterprise resource planning (ERP) software. This management software helps improve communications, streamlines operational processes, and provides business insights based on analytics. If you have a fleet of vehicles you might use transportation management software like Roserocket alongside that.
Supply chain management process steps
Here’s a look at the five main steps in the supply chain management process.
1. Planning and demand management
Forecasting customer demand is the first step in building an efficient supply chain that ensures product availability.
Typically, a demand forecast starts with collecting and analyzing previous sales data to project future sales. For instance, if your sales have been growing 10% month-over-month, you may predict that they’ll continue to do so for the next quarter or year.
Demand forecasts can also use external information, such as changes in customer behavior and macroeconomic trends. One example of a useful macroeconomic trend includes interest rates. When interest rates are low, that can lead to an increase in purchases that require financing, such as vehicles and homes.
Businesses then use these forecasts to inform their demand planning process. That is where you adjust orders and supply chain activities with the goal of achieving the right inventory balance.
You want enough goods on hand to meet customer needs but not so much that you end up with excess inventory.
2. Procurement
Procurement (also known as sourcing or supply management) refers to finding and purchasing the materials you need to meet your demand forecasts.
Sourcing activities include:
- Finding vendors.
- Ensuring the materials meet your product specifications.
- Negotiating prices.
- Acquiring the right amount of materials.
Once you’ve found your providers, much of procurement becomes monitoring supply and adjusting orders based on demand. But, most importantly, procurement involves building partnerships with key vendors.
Actions such as always paying on time, maintaining open communication, and giving them enough lead time help build stronger supplier relationships. By doing so, you create more opportunities for collaboration and identifying mutually beneficial opportunities.
As a result, your suppliers are more likely to prioritize your business and ensure your orders are always on time and meet quality standards.
3. Production planning
Your production strategy covers everything you need to do to turn materials into finished goods. That includes subtasks like manufacturing, quality control, and packaging.
At this stage, it’s crucial to reduce inefficiency and waste that can affect product quality, eat into profit margins, and slow down operations.
For instance, let’s say you have employees working machines without training. As a result, you may end up with more products that fail inspection that you must throw away. Over time, those manufacturing process inefficiencies can result in wasteful spending and long lead times. That's one of the reasons many growing manufacturing companies have started adopting digital solutions like cloud manufacturing software. It helps in increasing the efficiency of manufacturing operations by automating the production planning process.
4. Inventory management
The finished goods become your inventory once they’re ready to sell. At this stage, you still need to keep track of your products as they flow from manufacturing to storage and finally on to your point of sale (if you have a physical retail location).
In short, inventory management involves knowing exactly how much of each product you have and where your products are. It ensures a healthy balance between having enough product on hand without sitting on excess inventory.
Popular inventory management techniques include:
- Materials requirements planning: Involves filling in inventory as needed based on customer demand data.
- Just-in-time management (JIT): Requires working closely with suppliers and only having materials shipped right before you start production.
- Days sales of inventory (DSI): Involves optimizing inventory to reduce the amount of time that it takes to sell new products.
- ABC analysis: Involves prioritizing items that cost less to make and generate more revenue.
You can monitor your inventory manually. But technology like inventory management systems has replaced the traditional spreadsheets at many businesses.
These software solutions allow for improved efficiency and effectiveness. In particular, you can have real-time data visibility, which means you always know how much stock you have, and you can track the flow of goods through your supply chain.
You can also use process automation for tasks such as stock reordering, order fulfillment, and generating invoices.
5. Delivery and order fulfillment
Lastly, you have delivery and order fulfillment, which is the process of getting purchased items into the hands of your customers. For in-person customers, this step is simpler. It includes processing the order and payment and packaging the product.
However, online order fulfillment has become a growing priority for retailers — a 2022 Statista study valued the US ecommerce market at over $900B.
With companies like Amazon offering free two-day shipping for its subscribers, that challenges other brands to find ways to keep up with consumer expectations.
Retailers can choose from several fulfillment methods, including:
- Direct-to-consumer (D2C): You manage your inventory and handle all shipments to consumers.
- Stores as fulfillment centers: This method includes things like curbside pickup and buy online, pick up in store (BOPIS).
- Third-party logistics (3PL): You outsource your warehousing and fulfillment to a third-party distribution center.
- Dropshipping: You rely on manufacturers to ship products. Ecommerce stores that don’t manage inventory commonly use this fulfillment method.
From supply chain management to optimization
Supply chain optimization is a management approach that uses new technologies and other resources to ensure optimal performance and peak efficiency in the supply chain.
In this strategy, business owners or supply chain managers continually adjust relevant processes to eliminate wasteful spending, disruptions, and inefficiencies.
Here are some of the benefits you can receive from optimizing your supply chain strategy:
- Lower inventory and overhead costs
- Seamless customer experience
- More efficient processes
- Improved risk mitigation
- Better quality control
- Optimized shipping
- Better cash flow
The increasing digitization of supply chain planning and management has become more prevalent for optimization. A 2022 IBM survey found that 53% of chief supply chain officers (CSCOs) predict digital transformation will be the source of their competitive advantage over the next three years.
Here are a few ways you can use digital technologies to optimize your supply chain:
- Use Internet of Things (IoT) technology, such as RFID and sensor data to monitor your assets and track inventory as it moves from vendors to customers.
- Leverage enterprise resource planning (ERP) software to manage procurement, manufacturing, and supply chain tasks. An ERP combines data from several sources to enable better supply chain visibility, which helps you optimize inventory levels, generate better demand projections, and monitor supply chain disruptions.
- Consider adding warehouse automation techniques that boost efficiency by reducing congestion and optimize resource consumption. Implementing a warehouse management system can effectively streamline warehouse operations, contributing to enhanced overall supply chain performance.
Harnessing the power of new technologies and integrations can ultimately improve data-based decision-making, minimize supply chain risk, and foster more effective collaboration with suppliers.